Rubber materials are widely used everywhere. Applications range from classical tires over adhesives to road paving and toys. Depending on the composition, key features, such as viscoelasticity, vary significantly. The global demand of rubber materials is huge. The rubber tire market alone is expected to grow to a valuation of over US$ 190 Bn within the next couple of years and the global styrene block copolymer market size, for instance, is projected to increase by over 6 % by 2024. Innovative product development, which can be efficiently supported through modeling, is key for successful business growth.
The Challenge
Tires need to obey a wide range of requirements. Typically, fillers are used for achieving the desired performance. As they affect stiffness, tensile strength, and resistance to abrasion, amongst other key properties, it is important to understand how these properties depend on the composition. For these applications, a high stiffness is targeted to ensure longevity. On the other hand, other types of application demand elastic networks, which is realized by using unfilled rubbers or concentrated solutions of rubber-based materials like styrene/butadiene/styrene triblock-copolymers. For product design and development of high-performance and smart materials it is essential to know how properties are affected through the components.
The Work
Non-equilibrium dissipative particle dynamics (DPD) simulations using MAPS/LAMMPS DPD plugin have been performed on a cross-linked rubber with 20 volume % filler content. The filler was also highly cross-linked and chemically bonded to the rubber. A sinusoidal periodic shear was applied to the system and additional longitudinal strain simulations were performed to determine the key properties. Similar simulations were carried out on a triblock copolymer in a 50% tetradecane solution. The end blocks of the polymer were made from 70 monomers of styrene and the middle block of 570 monomers of Isoprene.
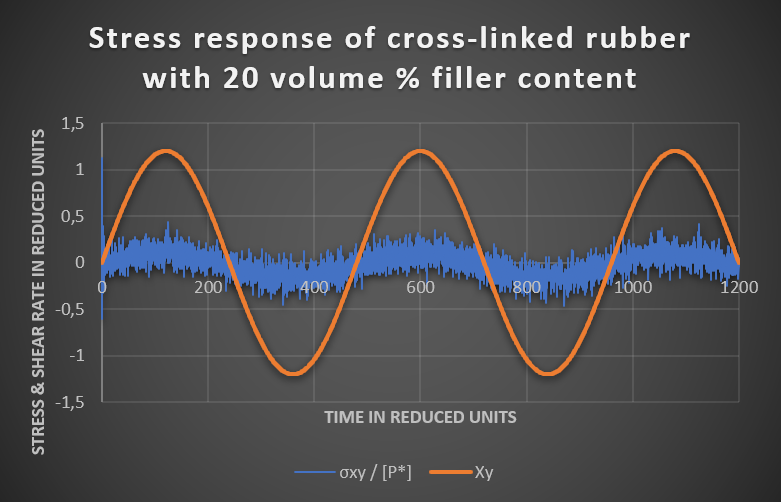
Figure 1. Stress response (orange) of the cross-linked rubber-filler system to an imposed shear (green).
The Results
In our studies non equilibrium DPD simulations with applied periodic shear or strain have been performed on particle filled rubbers and rubber-based adhesives. It has been proven, that both non-linear behavior of the composite systems as well as ideal elastic behavior of the additive systems can be captured by DPD simulations.
For the filled system, the storage and loss component of the dynamic shear modulus G were calculated from the stress response of the system. Also, the loss tangent (tan δ), the ratio between G´ and G´´, was determined from the simulations. At strains higher than 10% the system starts to flow, as longitudinal strain simulations have demonstrated.
These illustrative calculations show that modeling is capable to predict key properties of these commercially important materials and that in this way critical insight can be gained efficiently for supporting product development.