High-performance polymer composite materials have become increasingly important for numerous applications because of their advantages in weight reduction and energy saving. Thermosetting polymers are the matrices of choice for such composites because of their high stiffness, strength, creep resistance and thermal resistance when compared with thermoplastic polymers. These desirable properties stem from the three-dimensional (3D) crosslinked structures of these polymers. Due to their beneficial properties, these materials are undeniably attractive for a broad variety of applications in the automotive, aviation, wind power, construction or oil and gas market.
The Challenge
The three-dimensional network of bonds, i.e. cross-linking, makes thermosetting materials stronger than thermoplastic materials. The mechanical and physical properties of thermosetting polymers depend on their chemistry, composition, and curing conditions. Examples of cross-linked polymers include: Polyester fiberglass, polyurethanes used as coatings, adhesives, vulcanized rubber, epoxy resins and many more. Here, we present an in-silico approach for reproducing cross-linking virtually. Based on this, we examine how the cross-linking process of the thermosetting polymer epoxy EPON-862 and the curing agent DETDA affects the mechanical properties.
The Work
A simulation cell containg DETDA in EPON in a ration 1:2 was built using MAPS Amorphous builder. Cross-linking was performed starting from three different conformations, before applying a multistep relaxation protocol using molecular dynamics (MD) simulations. After relaxation of the newly formed bonds, tensile experiments were performed at an imposed stress rate of 1 atm/ps. Simulations were performed for a hypothetical ideal linear system and an 80 % cross-linked DETDA-EPON resin. Young’s modulus was obtained by analyzing the resulting stress-strain curves.
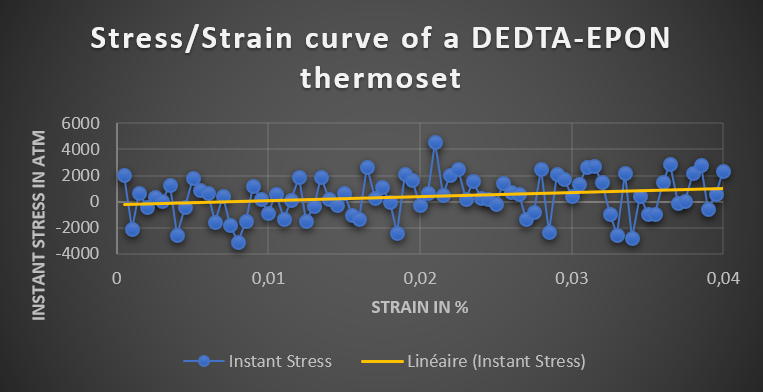
Figure 1. Stress-strain curve of a DETDA-EPON thermoset The fitting of the graph gives a Youngs modulus of 3.6 GPa which is in satisfactory agreement to the experimental value of 2.8 GPa.
The Results
A method for mimicking the cross-linking process of polymeric materials has been devised. It has been applied successfully on a DETDA-EPON epoxy system. Based on this, elastic properties of the thermoset have been calculated to study the influence of the cross-linking on the properties. Comparison with experimental results has been found satisfactory. The Youngs modulus of the crosslinked system shows to be more than a factor of two higher than the modulus of the ideal linear system. The developed simulation methodology can be applied to generate 3D cross-linked systems and is ideally suited to be used in workflows for systematically investigating how composition and cross-linking affects other relevant properties.